一、引言
温度循环试验箱在众多行业中扮演着极为重要的角色,其通过模拟产品在不同温度环境下的交替变化,来检验产品的可靠性与耐久性。而控制算法则是实现精确、高效温度循环过程的核心要素。本文将深入探讨温度循环试验箱控制算法如何对温度循环过程进行优化,以满足现代产品测试的严格要求。
二、传统控制算法在温度循环试验箱中的局限性
传统的温度控制算法,如简单的比例 - 积分 - 微分(PID)控制,在温度循环试验箱应用中存在一定的不足。在温度快速上升或下降阶段,由于热惯性和系统延迟,PID 控制可能导致温度超调或响应滞后。例如,在升温过程中,当设定温度发生较大幅度变化时,加热装置可能因 PID 控制的初始较大输出而过度加热,使实际温度超过目标温度,随后又需要制冷装置介入进行修正,这不仅延长了温度稳定时间,还增加了能耗并可能对试验样品造成不必要的热冲击。在温度循环的频繁切换过程中,传统 PID 控制难以快速适应不同温度设定值的变化,导致温度控制精度在循环过程中逐渐降低,无法保证每个循环周期内温度变化曲线的一致性。
三、先进控制算法的引入与原理
-
模型预测控制(MPC)
-
自适应控制算法
四、控制算法对温度循环关键环节的优化
-
温度上升阶段优化
-
温度稳定阶段优化
-
温度下降阶段优化
五、多算法融合与协同优化
现代温度循环试验箱往往采用多种控制算法融合的方式,以实现更全面、高效的温度循环过程优化。例如,将模型预测控制与自适应控制相结合,在模型预测控制的框架下,利用自适应控制实时更新模型参数和调整控制策略。在温度循环过程中,模型预测控制负责根据设定的温度轨迹进行长期的优化决策,而自适应控制则针对系统的短期参数变化和不确定性进行快速调整。这种多算法协同工作的模式充分发挥了不同算法的优势,既能够应对温度循环过程中的复杂动态变化,又能够保证系统在长期运行中的稳定性和可靠性。通过多算法融合,温度循环试验箱在不同的温度范围、循环频率和试验样品条件下都能实现的温度控制性能,为产品可靠性测试提供了高度精准且稳定的温度环境。
六、结论
温度循环试验箱的控制算法对于优化温度循环过程具有至关重要的意义。通过引入先进的控制算法如模型预测控制、自适应控制等,并实现多算法的融合与协同优化,能够有效克服传统控制算法的局限性,在温度上升、稳定和下降等各个关键环节实现精准控制。这不仅提高了温度循环试验的精度、效率和可重复性,还降低了能耗和设备损耗,为众多行业的产品研发、质量检测等工作提供了强有力的技术支持,推动了相关领域产品可靠性技术的不断发展与进步。
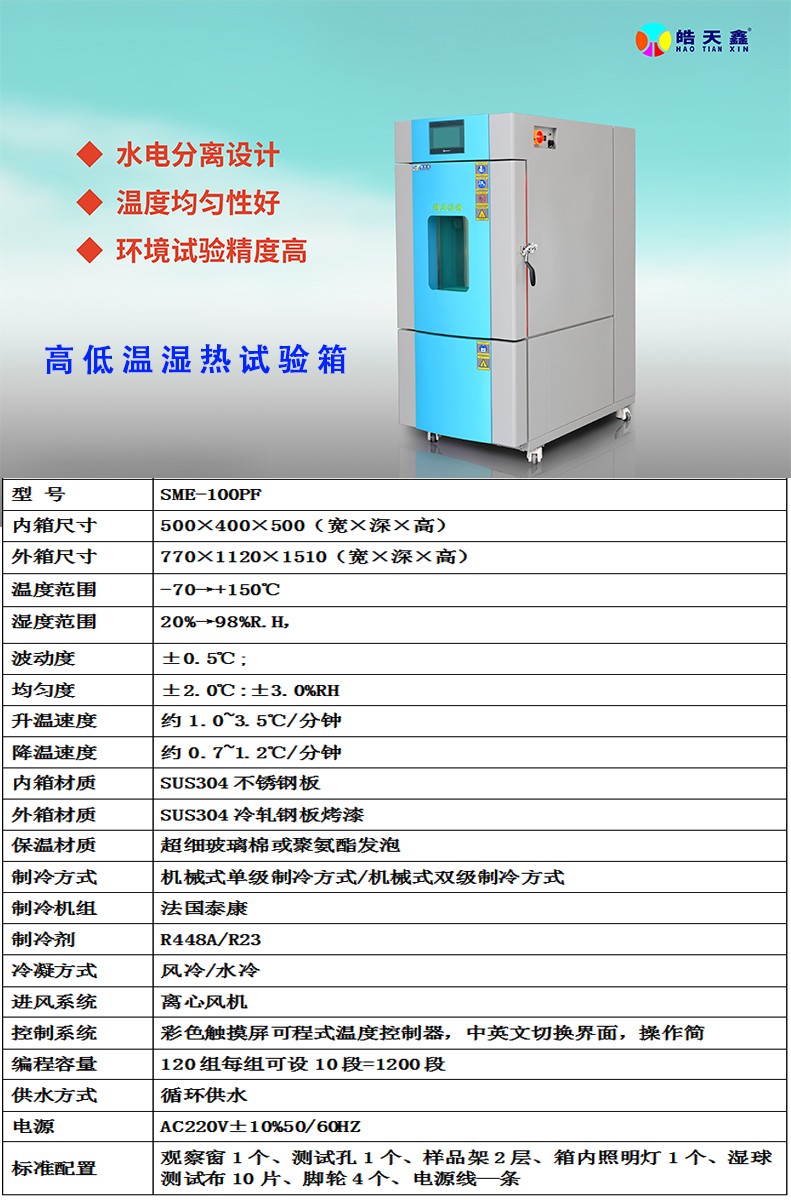